FULTON HOGAN TIMARU
ASPHALT PLANT DESIGN & BUILD
Fulton Hogan Timaru needed replacement parts for their asphalt plant, but didn’t have accurate plans to work from.
The designers at Real Steel worked with the team in Timaru to create precise 3D drawings of the parts they needed, which were then created from our high-performing Hardox® steel.
When Fulton Hogan Timaru dug out the old drawings for their wet scrubber water eliminator fan, it was soon obvious that creating the replacement parts they needed wasn’t going to be straight-forward.
The drawings were sent to the designers at Real Steel as a starting point, and after some back-and-forth with the tape measure over a few phone calls, the design team were able to finalise highly accurate 3D plans for sign-off.
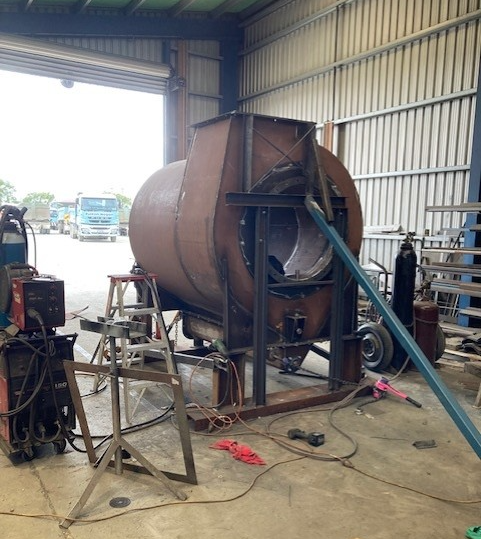
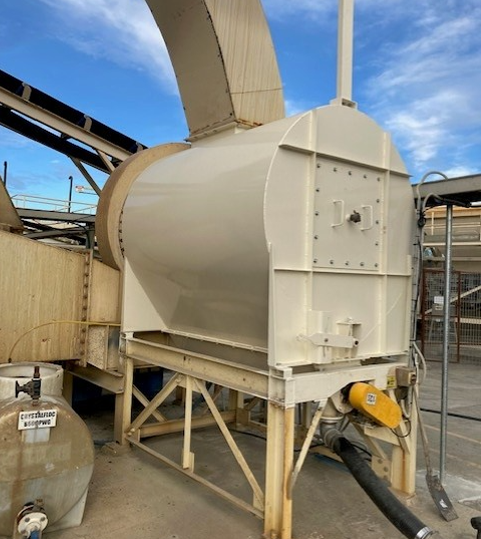
The replacement parts were immediately formed with Hardox® steel and shipped to Timaru in time for the Christmas shutdown period.
Over the break the Fulton Hogan workshop team craned out the old parts, and slotted in the new ones “without a hitch”.
They were back up and running for the start of the new year.
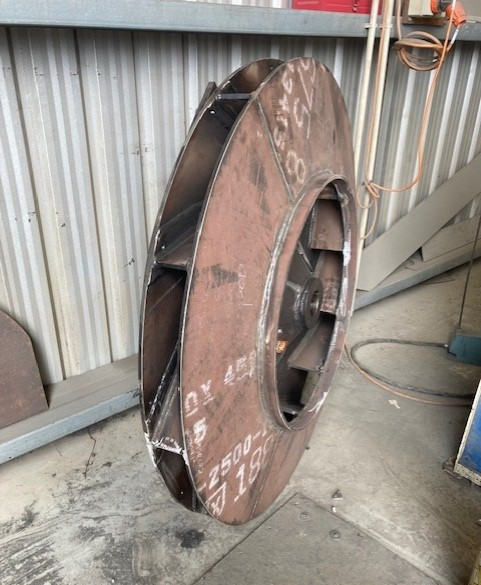
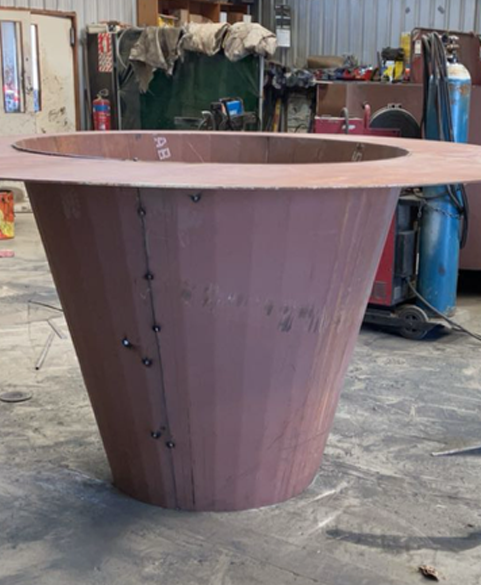
The feedback from the workshop team has been that “3D drawings are a game changer” when it comes to reverse engineering jobs like this.
The installation of the parts come together so much easier when they are designed and formed with the accuracy Real Steel can produce.
Learn more about our design-led process or get in touch with your local sales manager to find out how we can help.
DESIGN-LED PROCESS
Our team use SolidWorks software to build and analyse 3D models of your wear parts and other assemblies.
We accept only maximum accuracy – first time, every time.