AER ENGINEERING
FROM HARD FACE TO HARDOX EDGE
AER Engineering has gone from hard facing their loader edges, to welding on wear plate, and now to bolting on a formed Hardox plate.
The time and money saved by using the bolt-on approach has been undeniable.
In the past, Real Steel would hard face the base edge of all AER’s quarry loader buckets to minimise wear. This is a time consuming and expensive method, and puts a lot of heat into the steel which increases the chance of cracking.
More recently, we moved to welding wear plate onto the buckets. This was an improved approached, but still took considerable time.
With AER looking for a better option, we designed a formed plate of Hardox 500T that bolts onto the base edge without any welding .
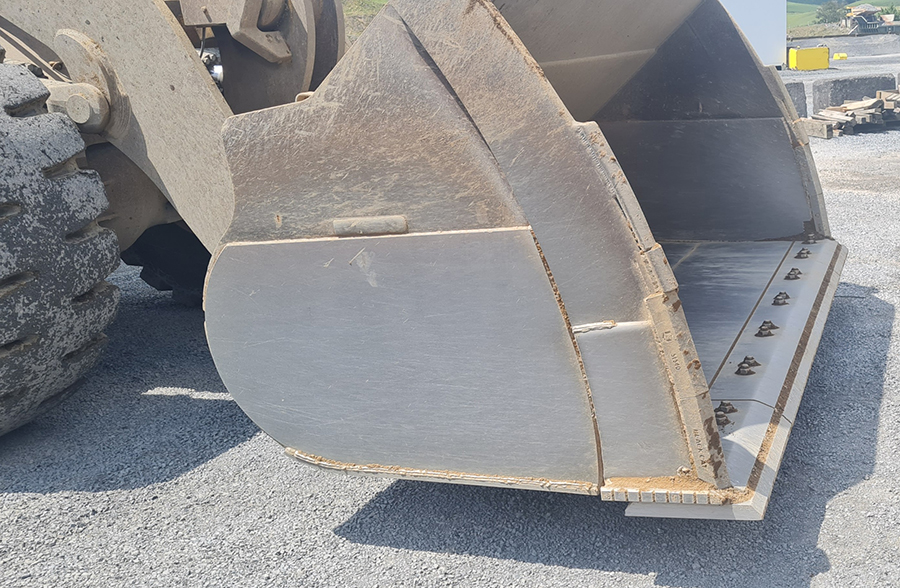
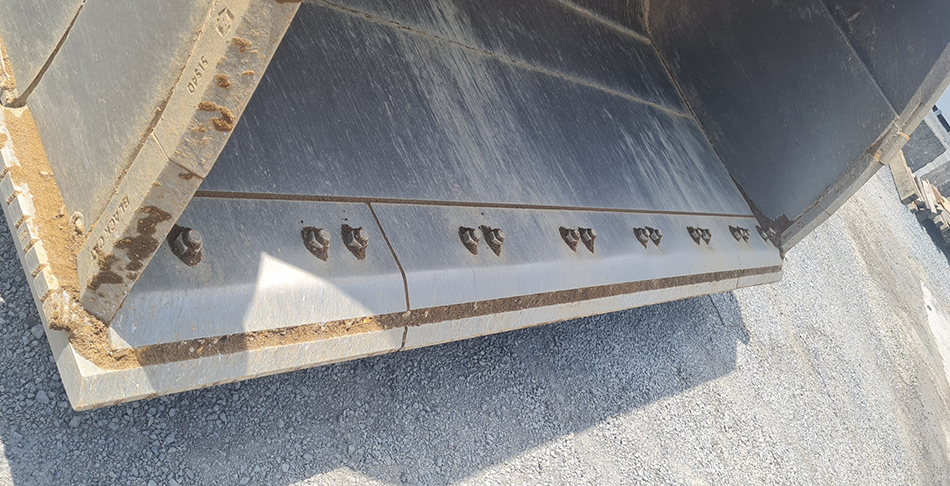
After more than a year using the new method, AER’s Jason Christie tells us he appreciates the ease of installation of the bolt-on approach.
The uniform and smooth coverage means less hang-ups – which makes for a more cost-effective option over time.
When the bolt-on wear plate is changed out, the original base edge underneath still looks like new.
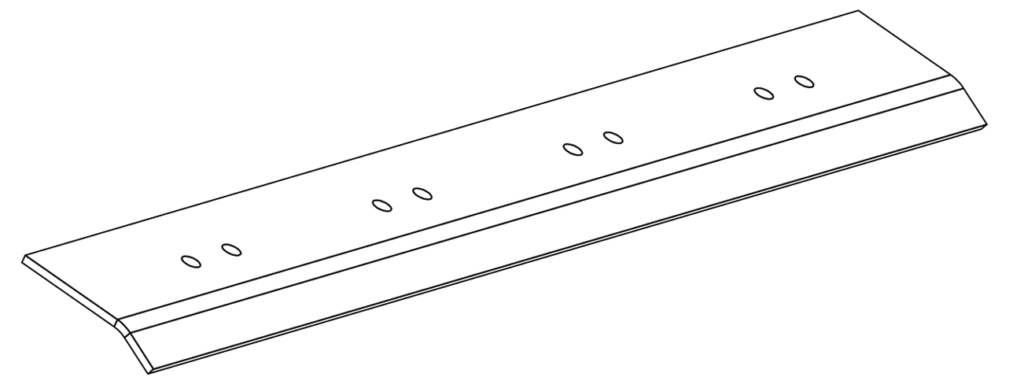